9 Nov 2010
Can Totnes and District House Itself? The potential of local building materials to build resilience
Here is a section from my recently completed thesis, which is available here, which looks at the potential of local building materials in the relocalisation process.
“The process of building with bales includes the possibility of making a profound change in the fabric of human societies around the world. In fact this vision is not exclusively a matter of straw bales: the questions we are trying to pose…. are basic: how do we build, and how does that process occur in relation to the community and to the life around us? Straw bales happen to be the material that has inspired many to look at the process of building in a different light”. (Steen et al.1994: xvi).
In the same way the local food movement shifts its focus from out-of-season, long supply chain, high embodied energy foods towards more locally sourced, low impact foods rooted in the local region or ‘foodshed’ (Kloppenberg et al. 1996), an emerging branch of architecture and construction examine similar transitions with building materials. The ‘natural building movement’ (e.g. Kennedy et al. 2001, Kennedy 2004, Woolley 2006, Broome 2007, Bevan & Woolley 2008, Jones 2009) argues that an architecture based predominantly on local materials is the most appropriate for a lower-energy context. Seyfang (2009) noted the evolution of the natural building movement from the ideas of Schumacher’s (1974) concept of ‘appropriate technology’, through to the Vales’ (Vale & Vale 1975) concept of the ‘Autonomous House’, to Pearson’s (1989) term the ‘natural house’.
She observed how, given the need for reductions in carbon emissions from buildings (around 50% of total emissions), there is a need to go beyond focusing solely on energy efficiency and building performance, and to look at the materials and techniques developed/rediscovered by the natural building movement to scale up. However, she noted “fundamentally different discourses, practices and governance of sustainability between the mainstream system of housing provision and green builders” (Seyfang 2009a:1), adding that “the challenge therefore is to better understand and therefore harness the creative energies of community-led solutions and adapt them for wider mainstream setting” (ibid).
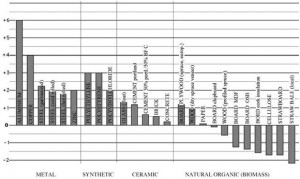
Figure 5.7. Overall CO2 emissions by weight (kg) released by production of 1kg of 24 common building materials (Source: MacMath, 2000).
The concept of using local building materials in a modern context is not novel. Seyfang (ibid.:3) wrote that “there has been a resurgence in traditional building materials which could be locally sourced from renewable or recycled materials such as strawbale, wool, cob (mud and straw mixtures), reed and thatch, as well as alternative formulations of concrete-using natural materials such as ‘papercrete’ and ‘hempcrete’”, due in part to an emerging recognition of the potential of such materials to lock up carbon, rather than to emit it (see Figure 5.7). A number of architects working in the developing world now argue that the use of local building materials offers the advantage of sustainable materials which produce healthier buildings while also strengthening the local economy. One of these is award-winning German architect Anna Heringer who has worked in Bangladesh to build a school, predominantly from earth and bamboo (Ashraf 2007:114).
Some commercial projects in the UK that feature local materials are already underway. The first Council houses built using straw bale construction, by North Kesteven District Council, are soon to be completed (Shah 2009), two Council houses were built by the Suffolk Housing Society in 2002 using hemp and lime construction (Clarke 2002) and a new school in Newquay, Cornwall, is to be built from cob (Yeoman & Taylor 2006). The challenge though, is that although these building techniques and materials have undeniable advantages in terms of embodied energy and healthy building, what is lacking, according to Seyfang (2009a:8) is “scaling up the existing small-scale, one-off housing projects to industrial mass production”. Also, most of the techniques require intense manual labour and tend to be built on one-off cheap rural sites rather than in urban development contexts. What is required, as Seyfang put it, is the natural building niche “adapting itself to resemble the regime” (Seyfang 2009a:8). This is starting to emerge with examples including prefabricated straw bale panels (MacKeown 2008), offsite construction (Sassi 2008) and hemp/lime construction (Bevan & Woolley 2008), although they still have some way to go before becoming a feature of mainstream construction. It is instructive to note, from the oral history interviews, how the shift from traditional natural building materials to modern industrial materials did not necessarily bring the benefits that it was hoped they would (see Text Box 5.8.).
Alan recalls his grandmother, with whom he and his mother lived, keenly moving out of an old house that was a converted cider press. “She just wanted modern. She wanted electric fires, electric cookers, electric everything. She wanted automatic this, that and everything. So we moved, at my grandmother’s insistence, from this wonderful rambling old building…. to a brand new house, typical of its time. Wooden framed, single glazed windows, open fire for a chimney which she quickly replaced with an electric fire, “I’m not having any more of that dirty coal business”. The winters were actually colder than the previous house! You’d wake up in the morning, and your breath would have condensed on the window, frozen on the inside. Inside it was cold, outside it was cold. Eventually my mother paid for an electric fire to be put in so you could reach out of the bed and turn it on. Electricity was cheap in those days”.
Text Box 5.8 The Energy Efficiency of Modern Housing in the early 1960s. (Source: author’s oral history interview with Alan Langmaid)
A recent paper by the Prince’s Foundation (Hulme & Radford 2010) explored the economic and social impacts on local economies that the move to building systems that utilised local building materials would deliver, in particular in relation to using locally manufactured aerated clay blocks. As well as analysing the potential of this one product, the authors reflect on the potential of scaling up the approach;
“Although this study only explored a single element of the building supply chain – structural clay blocks – these findings suggest that certain general lessons include tailoring construction techniques to local skills, designing building components which provide a range of secondary and tertiary benefits, and taking advantage of the positive impacts of simplified, generalisable approaches to complex, high-tech, specialised ones” (ibid:18)
The paper identifies a range of benefits that such an approach would bring:
- The simplicity of the systems means “it enables a local workforce to be used … this ensures that a greater proportion of economic value is captured in the local economy”
- Jobs would be created by the manufacturing of the materials
- It would also result in “professional skills development, a heightened sense of personal dignity and respect resulting from long-term professional employment, enhanced social well-being, improved social capital, healthier buildings, a more resilient building supply chain, reduced CO2 emissions, and increased longevity of the building stock” (ibid:15).
While many of the natural and local building materials and techniques outlined above have advantages from a Transition perspective, what has almost never been mentioned in the natural building literature is the potential for local materials in the retrofitting of existing buildings. Given that, of the country’s approximately 24 million homes, at least 87% are projected to still be standing by 2050 (Kemp 2010), and that retrofitting existing homes saves 15 times more CO2 than demolishing and rebuilding them (Jowsey & Grant 2009), this is clearly an important future focus. This theme of retrofitting is, however, picked up in the Prince’s Foundation paper; “beyond new build construction, a natural approach to materials sourcing means many of the products identified are equally suitable to retrofit in buildings of traditional construction” (ibid:19).
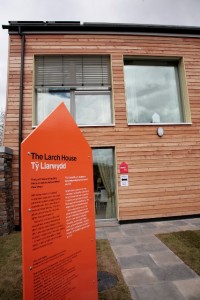
The recently completed 'Larch House', one of the two local Passivhauses.
Rob Scott McLeod, Technical Manager for the Building Research Establishment in Wales and the South West has been developing the concept of the ‘local passivhaus’. A passivhaus has been defined as “a building in which thermal comfort is guaranteed solely by re-heating (or recooling) the fresh air that is required for satisfactory air quality” (NBT 2009:2). McLeod is taking the idea one step further, seeking to build homes that reach passivhaus standard, but use predominantly local materials (McLeod 2007). Currently under construction in South Wales are two houses built to passivhaus standard, one of them using 80% local materials (mostly timber and recycled newspaper, ‘local’ here being defined as from within South Wales), and one aiming to go beyond 90%. The approach is one of on-site construction, site-specific design, minimisation of waste, and of a close coupling of design and materials (McLeod 2010:pers.int.). Some of the ‘natural’ building materials discussed above are not, as yet, felt appropriate for inclusion in such buildings, hempcrete due to not demonstrating sufficiently high levels of insulation, and strawbale due to not yet having sufficient certification to satisfy insurers. The key to reaching and exceeding 90% is training local companies to build windows to passivhaus standard using local timber, and this is already happening in South Wales as part of these projects.
The area of building and housing was explored in the TTT EDAP. It suggested how the current building standards could be improved and used to not just address carbon emissions but also to build resilience and strengthen local economies. One key element of this is what was called the ‘Transition Code for Sustainable Homes’. This suggests that by 2014, SHDC has taken a proactive stance of low carbon building, developing the Transition Zero Carbon Homes Code (see Table 5.4.).
Table 5.4 The Totnes Transition Zero Carbon Homes Code (Source: Hodgson & Hopkins 2010) |
|
Such an approach would lead to a more vernacular building style and opening up of a potential market for local manufacturing and processing of building materials. This principle of what Shuman (2008) called ‘import substitution’ would mean that money currently leaving the area for imported building materials would be retained in the local economy, creating new livelihoods and new small-scale industries. Some of the building materials that could potentially be produced within Totnes and district are identified in Table 5.5.
Table 5.5. A list of building materials that could be derived from the Totnes and district area (Source: the author, drawing from Clifton-Taylor 1987, Brunskill 2000 and from current natural building projects in the Totnes area and from historical precedents) | |
Timber | for construction grade timber, internal studwork, window and door frames, roofing shingles, laths, panelling, flooring, wattles, wood fibre insulation. |
Clay | for rammed earth construction, cob walling, daubs, clay plasters, cob bricks, clay paints |
Hemp | for use in hemp/lime construction, to make insulation, for hemp/lime or hemp/clay plasters and bricks |
Slate | for roofing |
Stone | for foundations, walls |
Reed | for thatching roofs, and also to make ‘reedboards’, an alternative to plasterboard |
Lime | for plasters, mortars, renders, as well as in construction systems such as hemp/lime |
Straw | baled, and used in ‘straw bale building’, chopped as an ingredient in plasters |
Sheepswool | insulation |
Horse hair/other fibres | used to strengthen plasters |
Recycled Materials | newspaper processed as an insulation product, car tyres, recycled bricks |
SP1 reflected on the practicality of such an approach of deliberately promoting and prioritising local materials through the planning process. He argued that, in the current context of planning driven by land availability and commercial viability, such restrictions would be unfeasible. “That’s quite a challenge”, he argued, “because the planning system isn’t all-powerful. It has to work within the government framework (i.e. Building Regulations, the Appeals process and so on), and of course you can set all those targets. However, you have to be confident that if a developer says “no, I’m not doing it”, you are able to defend it at a planning appeal, because if you make a hash of it you’re going to get pretty big costs against you”. He continued;
“[We can’t] say “you must use….” because then you almost create a ransom for the developer to be tied in with those local businesses. Now I don’t think you’d ever get that through the planning system, where you actually created a complete local monopoly because the developer would still want to go for value”.
Simon Fairlie, a planning consultant specialising in low impact development agrees that imposing ‘green’ conditions through the Planning System is close to impossible. According to Fairlie;
“At the moment even conditions imposing Code 3[1] are being overturned at appeal, because government guidance is so weak. Local materials would be resisted by builders as being “anticompetitive” and both a Tory or a Labour government would see it that way” (Fairlie 2010 pers.comm).
Some recent developments however offer the prospect of a more proactive, but less problematic approach to insistence on local building materials. The first is “the Merton Rule” introduced by Merton Borough Council in 2003, and widely copied in other council plans. It demands that at least 10% of energy needs must come from on-site generation, and comes into force at a threshold of 10 homes (residential) or 1,000m2 (non-residential). North Devon chose to demand 15%, and Kirlees Council are currently considering 30% by 2011, and the Merton Rule is now part of Plymouth’s Local Development Framework. The Merton Rule was sustained on appeal from the Building Federations which argued that it made developments commercially unviable. The Merton Rule is now endorsed in PPS1 Climate Change[2] which requires all UK local planning authorities to adopt a ‘Merton Rule’ policy. As Fairlie (ibid) points out, renewables are different from local materials, given that renewables can be sourced from anywhere in the world and hence circumnavigates concerns about ‘protectionism’ and lack of ‘competitiveness’.
The Merton Rule has since been incorporated into the Code for Sustainable Homes (CSH), which sets out the stages of the UK’s move towards zero-carbon housing by 2016. It includes the requirement for on-site generation which rises as the Code level rises, with the expectation that Code 6 buildings install “on or near-site zero carbon generation for all energy needs” (Hall 2008:89). In terms of building materials however, CSH is disappointing. It defines a ‘zero carbon home’ as one in which “net carbon emissions resulting from ALL energy used in the dwelling is zero” (DCLG 2008a:46), focusing on the performance of the final building rather than the carbon embodied in the materials.
If a legislative approach to scaling up the use of local building materials looks unfeasible, how about a criteria-based system? This, Fairlie (2010:pers.comm) argues, would “create an opening for best practice in places where conventional development would not be allowed”. The best current example of this is the Welsh Assembly’s ‘(Draft) Technical Advice Note 6. Planning for Sustainable Rural Economies’, published in July 2009. This presents the concept of ‘One Wales: One Planet’. It states that:
“the Sustainable Development Scheme, “One Wales: One Planet” includes an objective that within the lifetime of a generation, Wales should use only its fair share of the earth’s resources, and our ecological footprint be reduced to the global average availability of resources – 1.88 global hectares per person” (Welsh Assembly Government 2008:21).
This objective is then linked to planning, and in particular to the criteria that “planning applications should be accompanied by supporting information confirming that the development will be zero carbon in construction and use” (ibid:23). Fairlie notes that “priority for local, renewable building materials can be quite easily written into a policy like this, there are no anticompetitive issues, because it is a “consumer choice” rather than a trade restriction, and builders and other vested interests do not object” (Fairlie 2010: pers.comm).
There is a chicken and egg situation here though of course. If SHDC tomorrow were to pass a policy enshrining that a given percentage of materials were mandatory in all new buildings, there would not currently be capacity to meet demand. Conversely, nobody would invest in setting up such businesses without the knowledge that those markets will be in place. Hence the suggestion of a change in planning policy, flagged now, to come into effect in, say 2014. Perhaps the key is to begin developing buildings in the area that utilise these materials, in order to start creating demand and to lead by example, an idea explored in more depth in 7.4 in an exploration of the role social enterprise might play in Transition.
In terms of what is emerging through TTT and other local initiatives, some initiatives are starting to gain momentum in modelling this approach to construction. As with energy, housing projects are much higher capital and longer term, although some strong projects have begun to emerge. These include;
- The Totnes Sustainable Construction company, set up to pioneer these kinds of development
- Transition Homes, which is proposing to build a small settlement of low impact houses on the Dartington Estate
- ATMOS Project (see Section 7.9.), which aims to convert the derelict Dairy Crest site into a mixture of affordable housing and business start-up units
- Work is also beginning in relation to the drafting of a policy along the lines of those outlined above.
As Seyfang (2009a) notes, there is more to low carbon, community-led building than just materials. Other elements include what she calls ‘new living arrangements’, such as co-housing and low impact development, as well as the importance of communities owning and developing their own assets.
No questions specific to housing were asked in the survey or in the focus groups, although in the focus group of work and skills, unhappiness about the most recent large development in the town, the Southern Area development, and its low standards of energy efficiency, were voiced. One participant said “why did they put heating in those Southern Area houses? Why didn’t they make them energy efficient? All of them….” This was picked up in more depth in the in-depth interviews, which highlighted the fact that SHDC’s insistence on the lowest possible levels of energy efficiency in new buildings currently runs counter to the approach set out above. DC2 said “SHDC don’t impose the highest standards in new build, which I think disappoints a lot of us”. SP1 justified this approach when I asked him “the perception that is often voiced in terms of SHDC’s take on climate change and building standards is that rather than some other local authorities in the UK who take a visionary and bold stance, SHDC is happier taking the minimum set by Government?”
He replied that SHDC had tried to impose more stringent standards, but “you’ve got to make it viable. You can make your visions so challenging to deliver that nothing happens”. When asked whether actually taking a more stringent approach would mean that that would be precisely why businesses would want to come to the town, i.e. a selling point rather than just an insurmountable obstacle, he replied “yes, that could be a choice… my gut response would be that it would mean we had very little development in the town over the next few years. There’s an incredible pressure for housing in Totnes, and there are people coming through our reception facing homelessness. It is getting that balance between the vision and somebody facing homelessness today”.
SHDC’s approach is hardly unique. According to Gibbs et al. (1998), their approach is common. Sustainable development or environmental issues, they argue, appear to be a relatively unimportant concern for local authorities. Among the reasons cited for this are the limited influence local authorities are able to exert over private businesses and individuals behaviour, due, in part, to constraints imposed by central government. Sustainable development, they argued, is “a fundamentally political concept” (ibid:unpaginated). Ultimately, “creating and keeping jobs are ranked higher than environmental protection, and members remain to be convinced that the two areas are compatible” (ibid). Although written in 1996, the above could still apply to SHDC in 2010.
[1] The Code for Sustainable Homes was launched by the UK Government in April 2008, calling it “a step change in sustainable home building practice” (CLG 2008) It sets out 6 steps, Code 1 being relatively poor, and Code 6 being a ‘zero carbon home’, which it is intended that all new homes built from 2016 will be (Hall 2008:84)
[2] Planning Policy Statement: Planning and Climate Change. Supplement and Planning Policy Statement: December 2010 (CLG 2006). States its aim as being to set out: “how spatial planning should contribute to reducing emissions and stabilising climate change (mitigation) and take into account the unavoidable consequences (adaptation)”.
References
Ashraf, K.K. (2007) This is not a building! Hand-making a school in a Bangladeshi village. Architectural Design 77 (6). 114-117.
Bevan, R, Woolley, T. (2008) Hemp Lime Construction: a guide to building with hemp lime composites. IHS BRE Press.
Broome, J. (2007) The Green Self-build Book: How to Design and Build Your Own Eco-home. Dartington, Green Books.
Clarke, S. (2002) Client Report. Final Report on the Construction of the Hemp Houses at Haverhill, Suffolk. Suffolk Housing Society Ltd.
Fairlie, S. (2010) Personal Interview.
Gibbs, D, Longhurst, J, Braithwaite, C. (1998) Struggling with Sustainability: weak and strong interpretations of sustainable development within local authority policy. Environment and Planning A 30. 1351-1365.
Hulme, J, Radford, N. (2010) Sustainable Supply Chains That Support Local Economic Development. Prince’s Foundation for the Built Environment.
Jones, B. (2009) Building with Straw Bales: A Practical Guide for the UK and Ireland (2nd edition). Green Books, Dartington.
Jowsey, E, Grant, J. (2009) Greening the Existing Housing Stock. Sheffield Hallam University.
Kemp, M. (ed) (2010) Zero Carbon Britain 2030. Centre for Alternative Technology Publications.
Kennedy, J. (2004) Building without Borders: Sustainable Construction for the Global Village. New Society Publishers
Kennedy, J.F., Smith, M.G., Wanek, C. (2001) (eds) The Art of Natural Building: design, construction, resources. New Society Publishing.
Kloppenburg, J, Hendrickson, J, Stevenson, G.W. (1996) Coming in to the foodshed. Agriculture and Human Values 13 (3). 33-42
McLeod, R.S. (2007) Passivhaus – Local House. MSc thesis, University of East London.
McLeod, R.S. (2010) Personal Interview.
NBT (2009) Timber Frame System Passivhaus: the science of nature, the future of construction. Natural Building Technologies http://www.natural-building.co.uk/PDF/Pavatex/090216_Technical_Manual_PASSIVHAUS.pdf
Pearson, D. (1990) The Natural House Book: creating a healthy, harmonious ecologically sound home. Prentice Hall.
Sassi, P. (2008) Taking Construction off-site. In: Hall, K. (ed) 2008. The Green Building Bible, volume 1. Essential information to help you make your home, buildings and outdoor areas less harmful to the environment, the community and your family. Green Building Press.
Schumacher, E.F. (1974) Small is Beautiful: a study of economics as if people mattered. London, Sphere Books.
Seyfang, G. (2009a) Community action for sustainable housing: building a low carbon future. Energy Policy doi:10.1016/j.enpol.2009.10.027
Shah, D. (2009) Council to build houses of straw. BBC News. 20th January 2009. Retrieved from http://news.bbc.co.uk/1/hi/england/lincolnshire/8266515.stm on 22nd January 2010.
Shuman, M. (2008) The Small-mart Revolution: How Local Businesses Are Beating the Global Competition. Berrett-Koehler.
Steen, A, Steen, B, Bainbridge, D, Eisenberg, D. (1995) The Straw Bale House. Chelsea Green Publishing.
Vale, B, Vale, R. (1975) The Autonomous House. New York, Universe Books.
Woolley, T. (2006) Natural Building: A Guide to Materials and Techniques. Crowood Press.
John Boshier
11 Nov 12:59pm
“The best current example of this is the Welsh Assembly’s ‘(Draft) Technical Advice Note 6. Planning for Sustainable Rural Economies’, published in July 2009. This presents the concept of ‘One Wales: One Planet’.”
This is no longer in draft. It became law in July 2010, and lots of us are starting to discuss ways to put it into practice.
John Boshier
11 Nov 1:03pm
I’m just starting a Housing Group as part of Trawsnewid Calon Teifi in West Wales. This post is perfectly timed, and just what we need to be working on here.
Brad K.
12 Nov 5:06pm
Here in Oklahoma, USA, older buildings are routinely destroyed to make room for new uses.
The old buildings are very seldom salvaged at all. Not the windows, not the doors, not the lumber in the walls. Often cupboards and fixtures are left intact – just so much more rubbish.
My hope is that this practice comes to a screeching halt soon, as the cost of replacing usable salvageable materials becomes more costly than taking the time to salvage and sort the materials already on site, and local in the community.
And, please, someone, stop shipping scrap iron to China, so we can buy it back as new fasteners, new engines, and new spare parts.